Digital twin at a glance
Digital twin is a concept first introduced by NASA through the Apollo 13 mission of space exploration in the 1960s. The basic idea behind this concept was replicating voyaging spacecraft to create earthbound versions that allowed NASA Mission controllers to timely adapt and modify the simulations to match conditions on the real-life counterparts and adjust strategies to successfully bring the crew home safely.
In short, a digital twin can be understood as a virtual duplication of a physical object, system or environment. Being updated with real-time data and supported by simulation and machine learning, it is powered to look and operate in an identical way to its real world counterparts, which helps visualize what-if scenarios and anticipate potential results and issues to facilitate decision making.
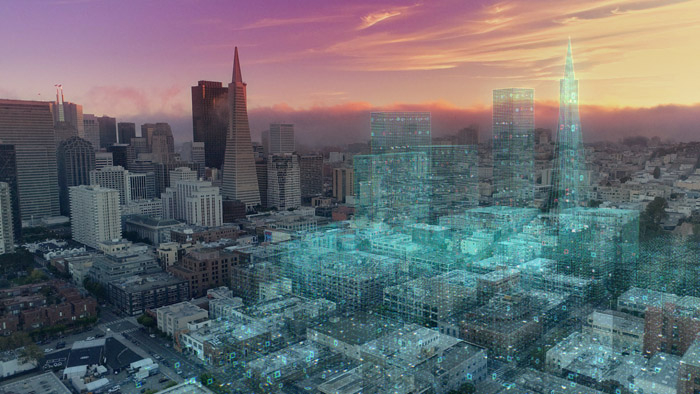
Following the bottom-up hierarchy, there are 4 types of digital twins with increasing levels of complexity along the way
- Parts twin or Component twin is the basic level of digital twin which provides physical, mechanical, and electrical characteristics of a part
- Product twin or Asset twin reflects how different parts interact with each other and their environment
- System twin or Unit twin brings an overview on the combination of different assets to form an entire functioning system to suggest improvements regarding operation and performance
- Process twin shows the connection of various systems to effectively create an entire production facility.
Application and benefits of Digital twin in the construction industry
Despite the fact that the construction industry is expected to be one of the largest in the world by 2030 as stated by Global Construction Perspectives and Oxford Economics, according to the Analytical report of the European Construction Sector Observatory, the industry is one of the least digitalized sectors in the economy.
It is widely accepted that the construction sector has long been facing various technical and management challenges such as low project performance, lack of skilled labor and other issues regarding sustainability and safety. As for that, digital twin technology has come to revolutionize the whole industry for both design and construction stage due to the ability to test all new assets within the stimulation before officially launching. By doing so, the safety, sustainability and performance of any buildings can be guaranteed at a certain level to minimize unwanted situations on actual construction sites.
In a BIM (Building Information Modeling) project, digital twins play a vital role in enhancing the analytical capabilities and as a result, bring a lot of benefits to the project teams as follows.
- Strengthen collaboration by a real-time and constantly updated two-way flow of data between the construction field and its virtual representation.
- Minimize risks due to the ability to make a test within the simulation before conducting any actual actions and spot potential faults with predictive analytics to timely prevent unwanted situations.
- Improve construction project performance thanks to better cooperation and effective resource and asset management
- Promote safety and security based on the modern monitoring systems and sophisticated sensors
- Optimize operation and maintenance phase by predicting the risk of structural failure and conducting appropriate remedial steps.
According to a report published by Markets and Markets, under the strong influence of digital transformation, the digital twin market is expected to grow to $48.2 billion by 2026. It is undisputed that digital twin contributes greatly to BIM capabilities. Especially with the strategic technology trends towards building smart homes and smart cities, digital twin can promise to transform the whole life cycle of the project in the construction industry as well as the urban modelling field.