Pushing the limits with a wooden skyscraper in Wolfsburg
Twice as ambitious: Sustainable and affordable
In Wolfsburg, the Woodscraper project is setting a new standard for sustainable and affordable construction in Germany. This 12-story wooden building is not only pioneering low-emission construction but also addressing the urgent need for financially accessible housing. With 106 apartments, half of which are allocated to low-income households, the project is backed by the client GLS Bank, a financial institution dedicated to sustainable investments and Unternehmensgruppe Krebs who developed the Project.
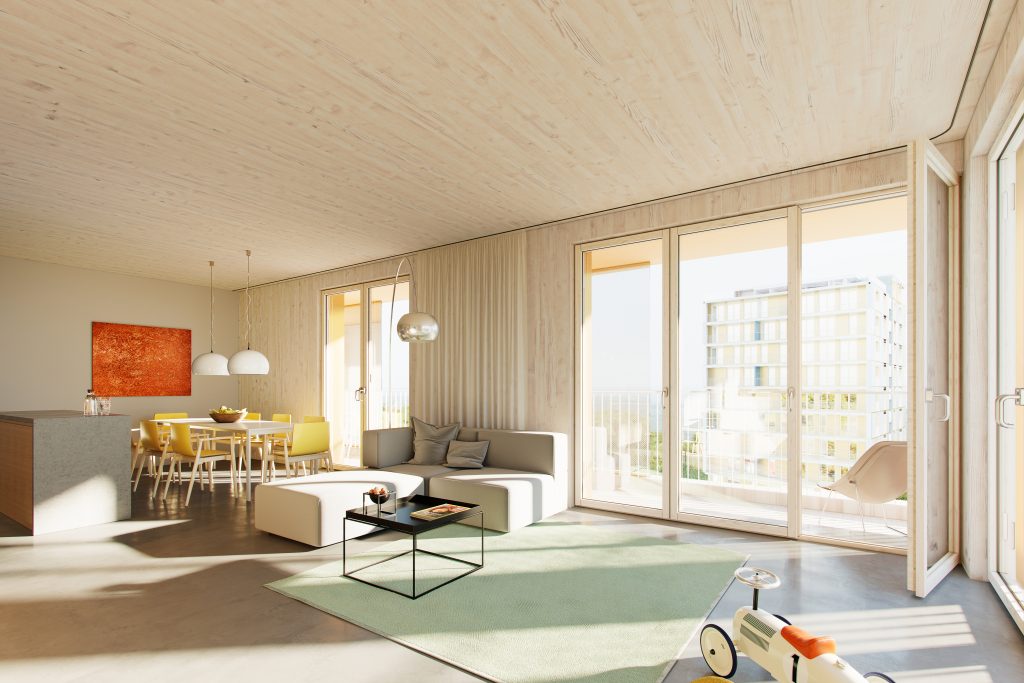
Scheduled for completion in late 2026, Woodscraper is navigating uncharted territory, overcoming regulatory gaps and technical limitations to demonstrate that large-scale timber construction is both viable and necessary for the future of urban development.
Jeroen Meissner, Architectural Project Leader at Partner und Partner, the project’s main designer and planner, takes us behind the scenes and shares his experience of this ambitious project.
More detail, earlier in the project
One of the key aspects Jeroen highlights is the meticulous attention given to the level of detail in the structural elements from the preliminary design phase (Leistungsphase 2). He explains:
“The design process for a timber construction is closely tied to the material’s properties, its
physics, and the production process.”
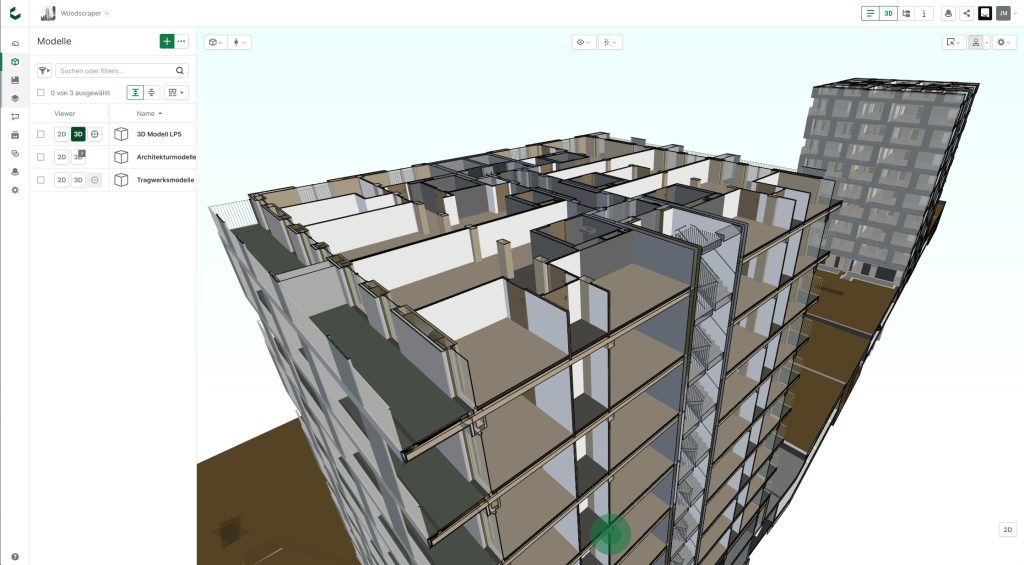
To ensure the Woodscraper was delivered on time and within budget, Jeroen, along with the fire protection and civil engineering teams, focused their efforts on refining measurements and level of structural details as early as possible. Their precision was essential in validating the feasibility of the design from the outset.
Shortfalls in current regulation and tools
Building a 12-story timber tower in Germany presents major challenges, as current building standards do not take full account of large-scale timber structures. Fire safety approvals had to be obtained on a case-by-case basis, making the process long and complex. Many ecological products for acoustic insulation also lack standardized guidelines, requiring extensive adjustments that add to project costs and timelines. While Building Information Modeling (BIM) is a key component of the design process, it does not yet fully support the needs of timber manufacturing.
“The wood construction company receives our 3D models, but they have to completely rebuild them from scratch because the BIM data from our platforms isn’t detailed enough for the machines that manufacture the wooden components.”
To keep the project on track amid the complexities of timber construction and evolving regulations, a structured and centralized system for sharing and managing information has become essential.
Saving time and maintaining project continuity
The team implemented Catenda Hub, a Common Data Environment (CDE) that streamlines collaboration and minimizes information loss. This solution ensured that every stakeholder—from architects to manufacturers—had real-time access to accurate project data, reducing inefficiencies and communication bottlenecks.
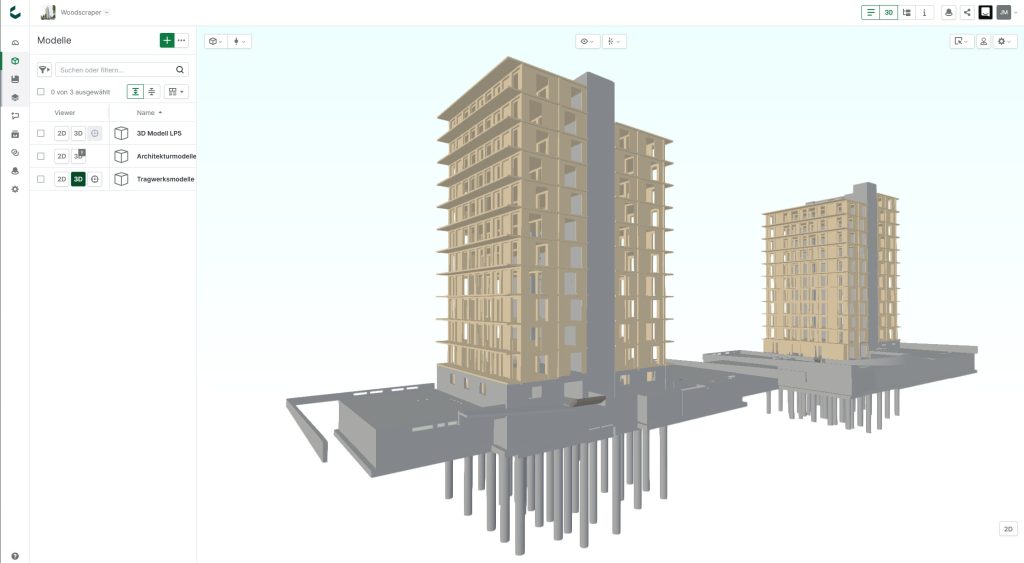
A real-life test proved its effectiveness when the engineering firm responsible for MEP and ventilation went bankrupt mid-project, forcing the team to find an urgent replacement. Jeroen Meissner explained that having a centralized data environment in place made the transition much easier, as all the necessary project information had already been structured and remained accessible.
“Because we had everything in Catenda Hub, we could quickly onboard the new MEP contractor, taking over from a contractor that unfortunately went bankrupt”
Beyond ensuring data consistency and accessibility, the use of a CDE such as Catenda Hub also saved the team valuable time by eliminating the need for constant email distribution and manual file exchanges. With all information structured and available in a single source of truth, the team saved hours each week that would have otherwise been spent searching for documents, resolving discrepancies, or following up on missing data.
A showcase for the future of wood in construction
By combining digital technologies, sustainable materials, and an economically viable model, Woodscraper lays the foundation for a realistic transition toward high-rise wooden buildings. If this project proves that such constructions are possible, it also highlights the immense challenges that remain.
“In this ambitious project, we could feel how hard and difficult it is to make a change in the construction industry,” says Jeroen Meissner. “The change is even more complex and difficult than we thought at the beginning.”
The regulatory landscape, the integration of new production technologies, and the financial dynamics of large-scale timber projects all present hurdles that cannot be ignored. Germany’s building norms, designed for conventional materials, add another layer of complexity.
“New construction techniques, products, and materials often don’t have all the necessary certificates to comply with regulations,” Jeroen explains. “Even when something makes sense from an engineering perspective, turning it into reality is still difficult.”
Woodscraper is more than a building—it is a statement. A first step toward proving that high- rise timber construction at scale is viable and attractive. Perhaps the success of Woodscraper marks a turning point in the industry, inspiring others to rethink how they build.
Screenshots: Partner und Partner Architekten