“The interface makes it easy to involve employees and customers in geographically dispersed projects that extend over a long period of time.”
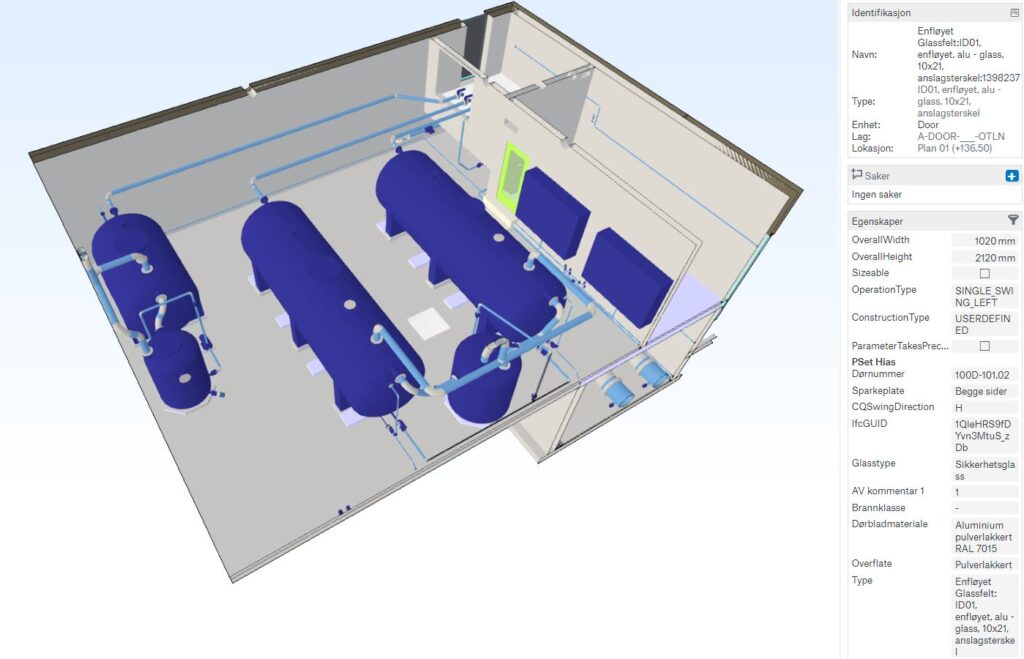
This is how Øyvind Seime from Asplan Viak describes Catenda Hub (previously Bimsync). Asplan Viak is currently involved in about 30 public projects in the field of water supply and wastewater treatment. Øyvind Seime believes that Catenda Hub (previously Bimsync) offers all participants a good opportunity for accurate, factual and transparent communication, especially for complex projects that usually extend over several years.
Norwegian water and sewage systems were largely built by past generations. In the coming years, Norway’s municipalities and provinces will have to invest considerable sums in order to renew them. It is difficult to estimate what it would cost to bring the facilities up to a modern standard that would meet the requirements of the future. The Oslo municipality, among others, has had a painful experience regarding this. Nevertheless, in the Association of Engineering Consultants’ report on the Norwegian water supply and wastewater treatment industry from 2019, the maintenance backlog alone is estimated at NOK 400 billion (approximately $46 billion).
This is probably the industrial field in Norway where there is by far the most that has to be done in future obligations, both in terms of the pipeline system itself and in terms of upgrading it to meet future water quality requirements. Current capacities are not sufficient. That is why a number of new plants are being designed and built throughout the country. Asplan Viak is involved in many of these projects. To date, the company uses Catenda Hub (previously Bimsync) for about 25 projects as a tool to accurately display what is being projected at any given time. “Among other things, Catenda Hub is used for interdisciplinary transparency, ease of display, decision making, and establishing a common and consistent baseline,” explains Seime.
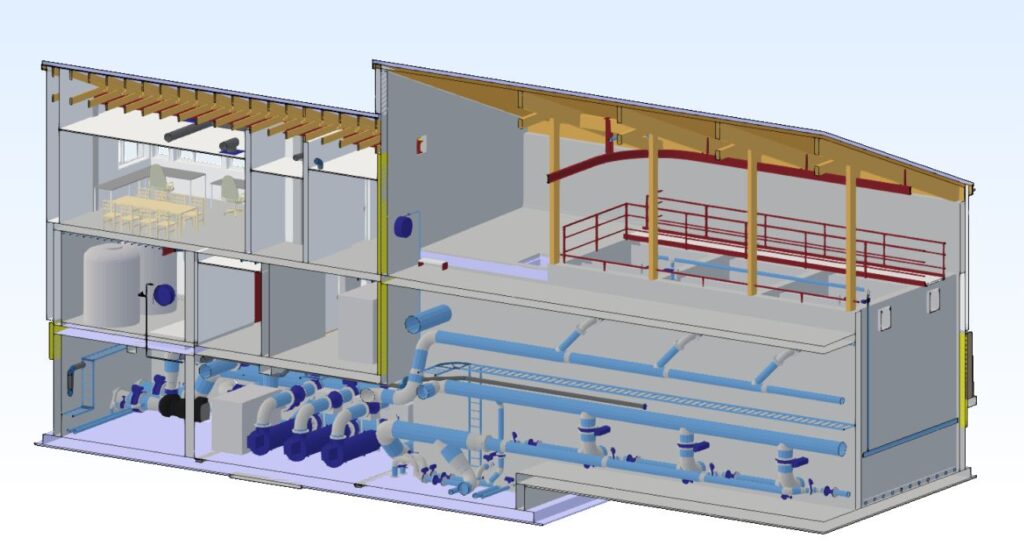
Large, complex and long-term projects
According to Seime, design and planning assignments for water supply and wastewater treatment plants are among the types of projects in Asplan Viak’s portfolio where the most internal expertise and resources are involved. In other words, the need for internal coordination is significant and is heightened by the fact that the organization is geographically spread throughout the country.
“When Asplan Viak designs projects for typical general contractors, for example for roads or buildings, we are handled quickly and accurately. In contrast, typical water and wastewater treatment projects can take five or ten years before they are ready to break ground, and involve many different phases with clients. These clients are often active in the process and want to contribute as much as possible to creating the best possible plant”, Seime says.
Taking care of what has been done
When different projects involve many people over a long period of time, there is a risk of losing experience, knowledge and practical skills along the way. People resign, change jobs or get other tasks, both internally and with the client. A holistic, solid, understandable and easily accessible interface of what has already been designed is therefore worth its weight in gold.
“Thanks to Catenda Hub, everyone involved gets a precise and clear presentation of the individual project in progress. The actors also have an overview and insight that allows them to easily involve the different resources, trades and areas of expertise. The “Common Data Environment cloud-based platform” (editor’s note) carries what has been established by the work in its entirety, and represents the project at any given time. Up-to-date, accurate and agreed upon. In addition, the number of email exchanges has been reduced along the way”, says Seime.
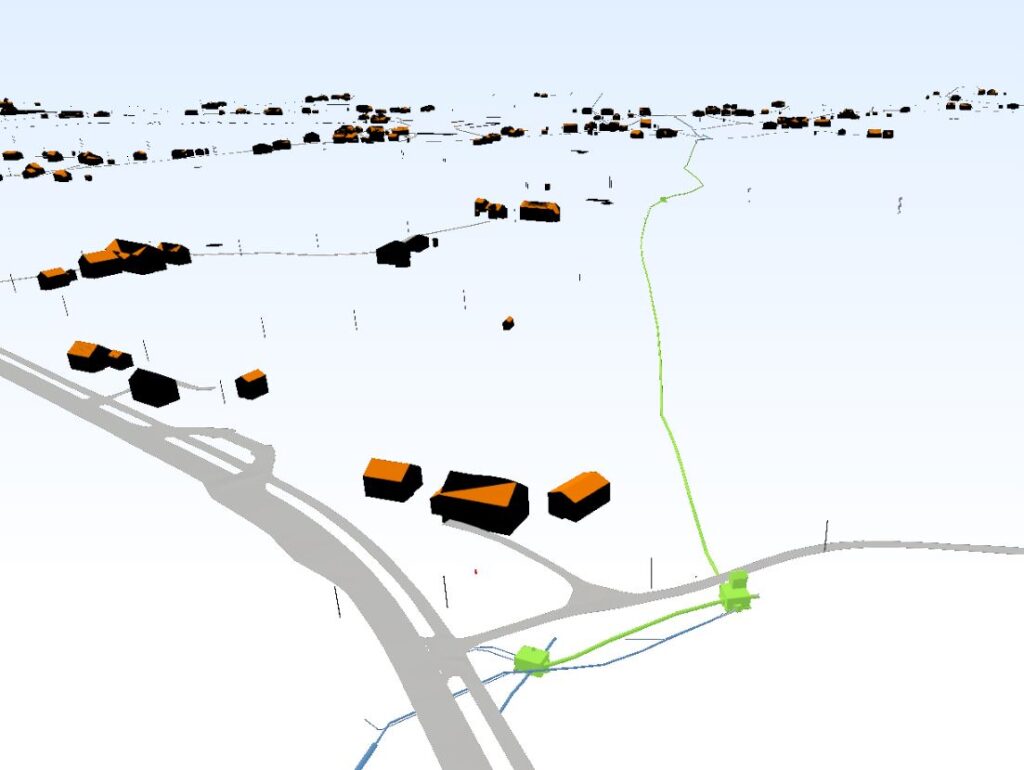
Intuitively accessible, regardless of skill or role
Seime, BIM coordinator and civil engineer, is well aware that large infrastructure projects abroad, e.g., the Paris metro, use Catenda Hub (previously Bimsync) as a Common Data Environment (CDE) platform where all the different shop drawings are collected and compiled. But he points out that at Asplan Viak, other solutions have been chosen for the supporting documentation itself.
“We use Catenda Hub (previously Bimsync) as a common data environment that is constantly updated, with the aim of making all the information available in a simple way to the people involved. This is of course beneficial for those who design and model. However, in projects like this, many of our employees with other tasks are still drawing in 2D. Thanks to Catenda Hub’s easy to use platform, the team members also have access to detailed discussions and decision documents. This documentation is actively used in the ongoing process toward the client, and makes all discussions concrete, fact-based and insightful,” says Seime.
Available to anyone, everywhere
According to Seime, a big part of the appeal is that Catenda Hub (previously Bimsync) is 100 percent cloud-based. There is nothing to download, and also nothing to install or update. Anyone who needs access just needs the project link.
“For us, internally, this ease of access may not be so important, but for a customer it is priceless. Everyone connects when they want, from where they want. The information is accurate and understandable. You can see the whole installation, how it looks on the ground and you can go to certain areas and see them, including solutions and details. This has allowed us to get much better information from the customer. It’s clear that Catenda Hub opens the door to a completely different form of communicating interest, understanding and participation in design”, Seime says.
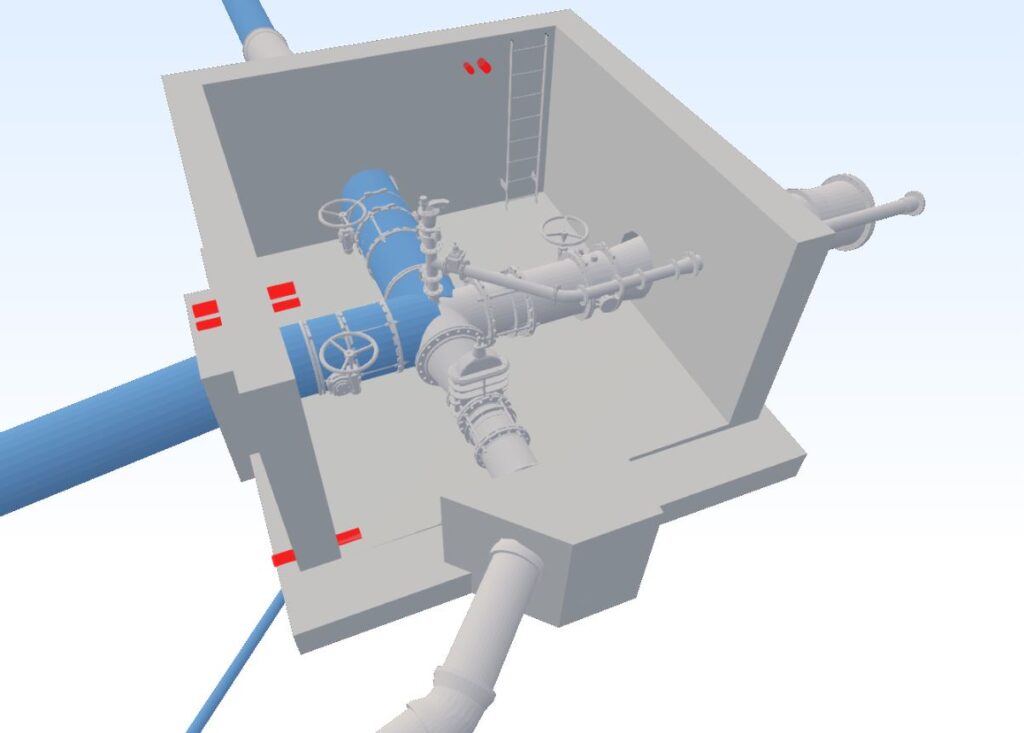
Reusing real user experience
Seime and the other members of the design and planning team also note that the customer’s priorities have changed dramatically. It used to be about the actual “delivery,” which often consisted of drawings and explanatory notes. But now the focus is more on the model to ensure an optimal product.
“Ultimately, what we create must excite and inspire those who must have it as a workplace. As before, our customers are represented by a project team and a project manager, but also with the help of the actual maintenance and operations staff. A reference team that does not necessarily understand or have the prerequisites to provide constructive feedback based on cryptic drawings, but has a massive amount of useful information, in-depth experience and practical knowledge related to the task that the given facility has to fulfill. With an easy to understand digital presentation of the final plant, their important input is now at the heart of the design”, Seime explains. “If we can deliver good plants, where the customer feels they have been involved in the choices made and have contributed to them, I think we will have more satisfied customers!” Seime says.